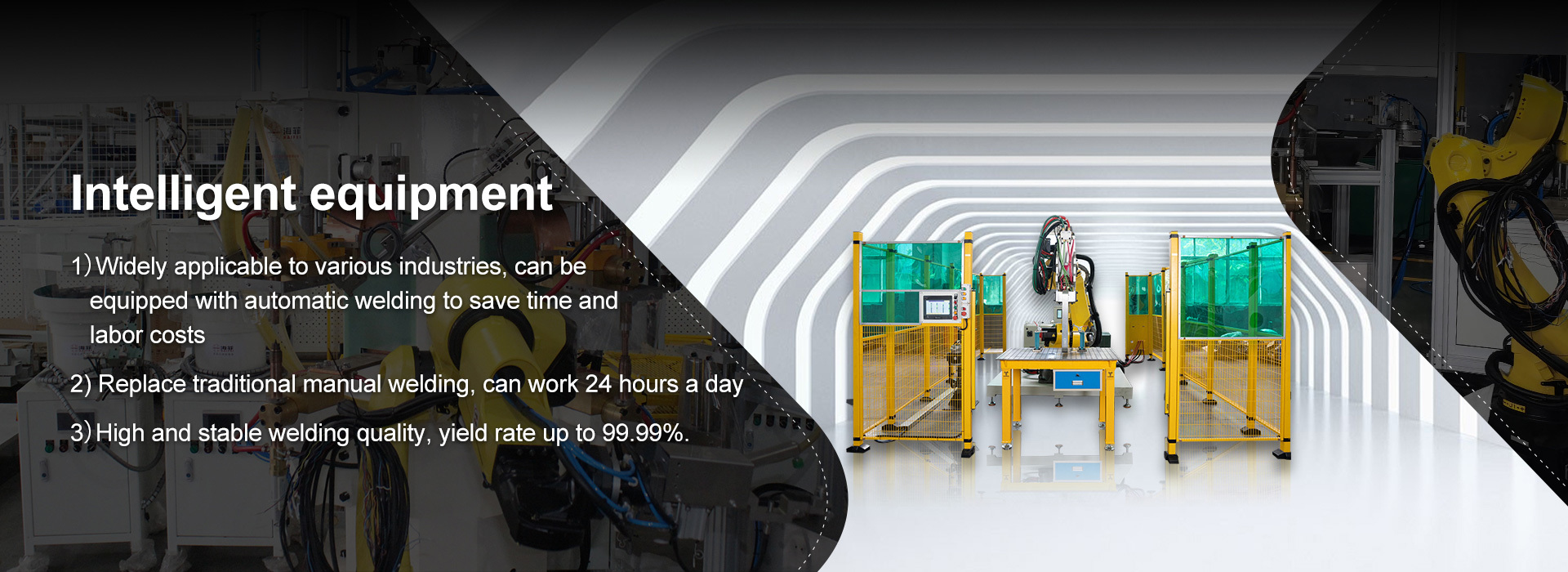
Robotic Welding System
What is robotic welding?
Robotic welding is a process that utilizes automated machinery, known as robots, to perform welding tasks and helps the industrial sector to increase accuracy, enhance safety and reduce lead time. It is a highly efficient and precise method of welding that has become increasingly popular in the manufacturing industry.
When a welding process is automated using robots, we call it robotic welding. These building robots perform and manage welding tasks based on the program and are capable of being reprogrammed as per the intended project. However, this does not eliminate human intervention as welders still control and supervise the welding robots.
What are the types of robotic welding?
The main types of robotic welding include:
Spot welding
Resistance welding
Arc welding
MIG welding
TIG welding
Laser welding
Plasma welding
Each type has its own unique advantages and is suitable for different applications.
What are the benefits of robotic welding?
Robotic welding offers numerous benefits such as increased productivity, improved quality, reduced waste, lesser labour, lesser costs, time-efficient, and enhanced safety. It also allows for greater precision and repeatability compared to manual welding.
What are the challenges and limitations of robotic welding?
Despite its many advantages, robotic welding also presents certain challenges and limitations. These include the high initial cost of equipment, the need for skilled operators and programmers, and the difficulty of welding complex or irregular shapes.
What are the components of a robotic welding system?
A typical robotic welding system consists of several key components, including the robot arm, the welding torch, and the power supply. Each component plays a crucial role in the welding process.
Ideally, robots can weld in any industry that has welding applications. The most common industries for robotic welders are:
Automotive
Aerospace
Metals
Construction